Plastic Injection Molding
home / capabilities / plastic injection molding
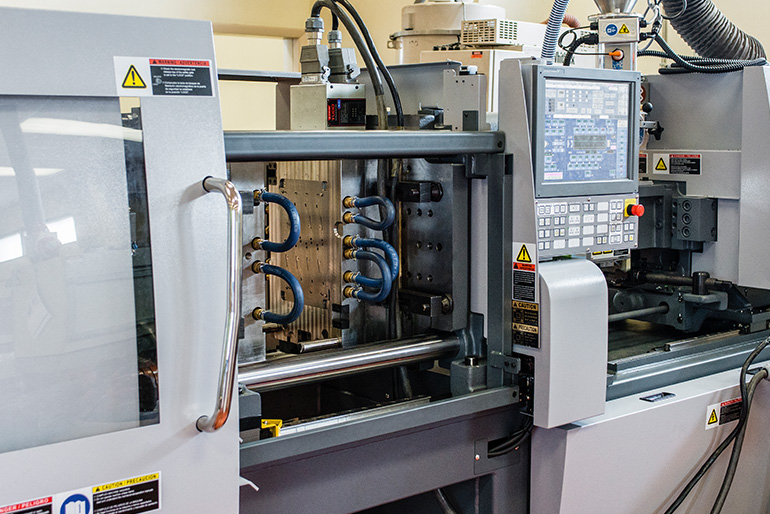
Expertise with Complex Products
Cadrex has been a leader among plastic injection molding companies for over 50 years. Our early engineering involvement allows us to mitigate product design issues and costs during the new product introduction (NPI) process while decreasing time to market.
Our experience tackling complex product design, temperamental specialty materials, and intricate tool builds makes us an ideal plastic injection molding manufacturing partner for your next program. With our state-of-the-art plastic injection molding machines in Mexico and across the United States, Cadrex is the premier plastic injection molding manufacturer in North America. You can count on a dedicated team of experts to work with you throughout the product lifecycle, assisting with initial parts discussions and the production launch.
Injection Molding Capabilities
- 36 Injection Molding Machines
Plastic injection molding machines are categorized by tonnage, or the amount of force it takes to hold the mold shut. Horizontal molding, performed on a machine that opens and closes on a horizontal path, is the most common type of molding where parts drop into a box or onto a conveyer belt. In contrast, vertical molding is ideal for overmolding or insert molding because gravity helps the part being overmolded stay in position.
- Clamp Force 28 Tons - 950 Tons
The clamp force is the force needed to keep the mold closed while it is filled with plastic. Read our plastic injection molding glossary.
- Engineering & Commodity Grade Resins
Commodity grade resins are often less expensive and easier to process than other plastics. They are the most common type of plastic molding material, can be easily mass produced, and are used for a wide variety of consumer goods. Engineering grade resins are plastics that are designed to withstand specific conditions, giving them qualities like high heat resistance, chemical resistance, or strength. Companies that produce materials for injection molding will design custom resins that are formulated to meet specific application requirements.
- Plastic and Metal Overmolding
Overmolding is the process of molding one plastic over top of another plastic or metal component. It is used to create strong material bonds and to improve the functionality and appearance of an item. Learn more about plastic and metal overmolding.
- Structural Foam Molding
In structural foam molding, a foaming agent is mixed with resin, the mixture is injected into a mold and heated into a gas, and the gas forms a thick skin on the inside wall of the mold. The process uses less material and creates lighter parts than other molding processes. Learn more about structural foam molding.
- Insert Molding
Insert molding involves placing preformed parts or metal inserts into a mold, where molten plastic flows and hardens around the object. Insert molding services often eliminate the need for post-production assembly and ensure a tight bond between the plastic part and its inserts. Learn more about insert molding.
- Pick & Place Automation
Pick-and-place automation uses a robot arm that can pick up an item and place it in another spot. This method is often used in CNC machining and for producing parts at high volumes. Learn more about BI, automation, and robotics at Cadrex.
- Robotic Operators & Conveyor Systems
Robotic operators and conveyor systems work together in plastic injection molding machines; the conveyor system takes parts to and from the robotic operator, which moves the part through the injection molding process. Learn more about BI, automation, and robotics at Cadrex.
- Post-mold Machining
Post-mold machining is work performed on injection molded parts to give them their final shape, improve their appearance, and provide additional properties (like enhanced strength or durability). Our expanded precision machining capabilities provide the potential to complete or assist in the production of a part when paired with plastic injection molding.
- In-House Tool Design and Maintenance
Every custom injection molding project at Cadrex is designed for manufacturability and excellence. Our designers collaborate with your team and engineers early in the prototyping and NPI process to address obstacles that may arise and opportunities to improve cost and quality. Learn more about engineering and prototyping at Cadrex.
- Conveyor Paint Line, Pad Printing, & Silk Screening
Cadrex offers a myriad of mechanical assembly and finishing solutions, including conveyor paint line systems, pad printing, and silk screening. Products move through a conveyor paint line for finishing applications, like coat paint, powder coating, or wet spray. Pad printing is the process of transferring a 2-D image onto a 3-D object or part. Silk screening is a method of transferring ink or dye onto a base material or fabric around a stencil.
Increased Efficiency
Injection Molding Automation
Cadrex's plastic molding operations incorporate multiple forms of automation and robotics, including custom fixtures to increase efficiency, quality, and ergonomics. Depending on our customers' program requirements, we have the expertise to incorporate pick-and-place automation or a robotic operator for faster and more consistent cycle times, better labor utilization, and lights-out manufacturing.
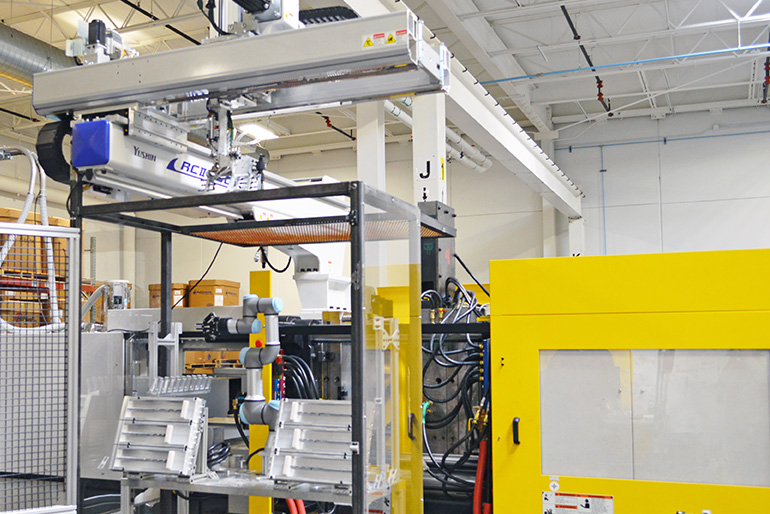
How it Works
Plastic injection molding is the process of injecting plastic material into the mold cavity of a metal tool, which then cools and ejects a plastic part from the machine. Most plastic products we see and use daily are made using this manufacturing process.
Plastic injection molders, or machine operators, load resin, a generic term for plastic material, into a plastic injection molding machine in the form of a pellet. A screw, called the reciprocating screw, rotates the plastic into a heated barrel. Friction and the heated barrel melt the plastic, which accumulates in front of the screw. The screw then pushes the molten plastic through a nozzle into the mold, where cooling channels help it cool and harden. The mold opens after a predetermined cycle time, and the machine ejects the plastic part and repeats the process.
Uses of Plastic Injection Molding
Products made from plastic injection molding are found everywhere from the car in your garage to the kitchenware in your cabinets and bottles of water in your refrigerator. The manufacturing process allows for high production rates and repeatability at a low cost per part. Therefore, it is often the best choice for packaging, plastic parts, and disposable medical devices. The flexibility and properties of plastic make this a solution when creating mechanical parts, casings for electronics, and construction materials.
Common Injection Molding Materials
Engineering Grade
Acetal (POM), PBT/PET (GF & Non GF), PC/ABS, PC/PET, Polyamide (Nylon 6 & 6/6) (GF & Non GF), Polybutylene Terephthalate (PBT), Polycarbonate (PC), Polyether Ether Ketone (PEEK) (GF & Non GF), Polyether Imide (PEI) (Ultem), Polyethylene Terephthalate (PET), Polyphenylene Ether (mPPE), Polyphenylene Sulfide (PPS), Polyphthalamide (PPA) (GF & Non GF)
Commodity Grade
Acrylic (PMMA), Acrylonitrile Butadiene Styrene (ABS), Polyethylene (PE) (HDPE) (LDPE), Polypropylene (PP), Polystyrene (PS) (HIPS), Styrene Acrylonitrile (SAN)
Injection Molding Design Guide
Learn more about the injection molding process including terms, definitions, and industry best practices.
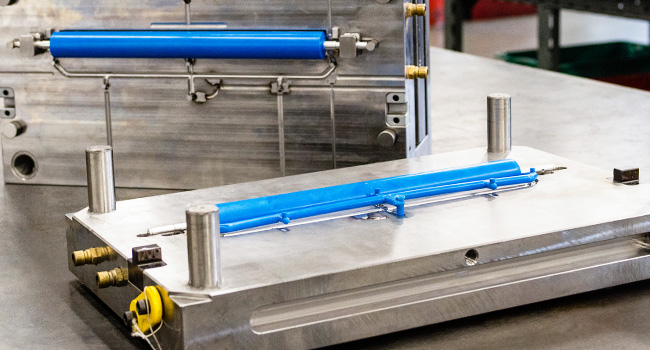
Tooling Design & Build
Our highly talented injection molding tooling engineers can design simple and highly complex single-cavity, multi-cavity, and family tools. Actions can be built into your tool depending on the complexity of your injection molded part to ensure you get the look and function needed.
Our plastics operation utilizes domestic and international suppliers for the tool build, which our in-house engineers closely monitor. We constantly communicate with our suppliers to keep your tools on schedule and monitor quality. Maintenance and repairs are taken care of by our in-house tool room.
Related Links
White Paper
A Starter Guide To Injection Molding
It is easy to brush over the basics of plastic injection molding and start talking about the benefits, especially when...
Blog
Plastic Injection Molding Design Tips
When designing a product, it’s easy to create something that fits all requirements for the product's intent without any thought about the manufacturing process. Many times, it might not be clear what manufacturing process...
Blog
Transitioning Outdoor Electrical Enclosures And Fiber Optic Boxes To Plastic
Designing outdoor electrical enclosures or fiber optic boxes? There might be some excellent reasons to switch from metal to plastic, but it’s a good idea to first talk to a manufacturer that does both....