Our customer needed help testing the water resistance of a large electric vehicle (EV) charging station structure, as well as pinpointing non-functional parts to speed up assembly. Our engineers and production managers came together to offer a solution.
The Problem | COMPANY Technologies needed to identify non-functional parts of an electric vehicle (EV) charging station structure (for which Cadrex supplied dozens of parts) to speed up assembly and production. The customer also wanted to test the water resistance of the structure, which would be subject to the elements in its placements. At nearly eight feet tall, the height of the structure made waterproofing and leak testing difficult.
Thank you Cadrex team for the outstanding support and service provided during our experiment Without your support, the team could not have gone that extra mile.
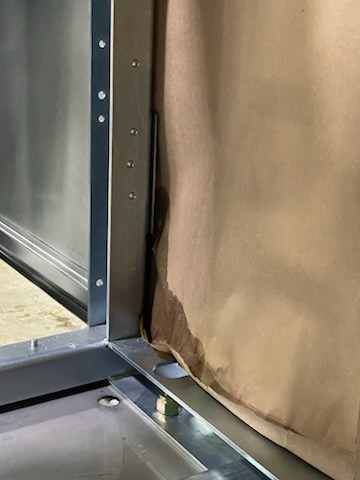
The Solution | Experts from several Cadrex locations joined representatives from COMPANY to assemble the parts and check for any issues. They designed a water ingress test to see how much water could enter the shell of the charging station. For the test, paper was affixed to the enclosure to use as a moisture indicator while water was directly applied for 15 minutes on all four sides of the unit. The paper indicator was then visually inspected to identify areas of water intrusion.
The Results | The test concluded there was no significant water penetration (the paper indicator remaining 99 percent dry), and there were no significant quality problems. The test also provided the customer with valuable product feedback by identifying areas where the customer missed some silicone application and gasket around the hinges (picture). We also helped them pinpoint non-functional parts; by avoiding having to rework unnecessary parts, they could speed up assembly. The response to this test was overwhelmingly positive and appreciative. From the customer: "Thank you Cadrex team for the outstanding support and service provided during our experiment… the team has shown true dedication and determination. Without your support, the COMPANY engineering team could not have gone that extra mile. A massive thank you to each one of you. The time and effort that you have put in is just amazing."
Recent Case Studies
Case Study
Example Case Study Title
Excerpt.....
Case Study
Example Case Study Title
Excerpt.....
Case Study
Example Case Study Title
Excerpt.....