Blog
Transitioning Outdoor Electrical Enclosures And Fiber Optic Boxes To Plastic
Designing outdoor electrical enclosures or fiber optic boxes? There might be some excellent reasons to switch from metal to plastic, but it’s a good idea to first talk to a manufacturer that does both.
September 17, 2021
Whether you live in an apartment building, a home in the suburbs, or that big, beautiful house on the hill, there’s one thing that none of us can live without: electricity. And while it’s often ignored, one of the critical components needed to deliver this electricity is the junction box hanging on the side of practically every building in the country. It’s here that the heavy gauge wire from the street gets split into the smaller electrical runs used to power the toaster, refrigerator, TV set, and other modern-day conveniences with which we are all familiar. At the risk of sounding like Captain Obvious, without electrical boxes, we’re in the dark.
Making Connections
Similarly obvious statements can be said about many of these outdoor applications. These include the fiber optic termination boxes seen on the outside of large commercial facilities and schools, and at the ends of long cable runs from our internet service providers (ISPs). As with the household electrical example just given, underground fiber optics cable containing dozens or perhaps hundreds of strands feeds into these junction boxes before being connected to splice trays for distribution to the consumer. To anyone surfing the Internet or binging on Netflix, these robust fiber connections are every bit as important as online pizza delivery.
Such connections will soon be even more important. As 5G technology expands over the coming years, these splice boxes and other types of fiber infrastructure will become increasingly necessary to meet our population's demand for high-speed Internet and cellular communications. And while nationwide fiber optic deployment promises to be a massive undertaking, just as critical is the need to manufacture gazillions of fiber enclosures. The question then becomes: what’s the best way to cost-effectively produce these components?
While we’re on the topic, it might be time to ask the same question about the electrical boxes and other fabricated enclosures just mentioned, particularly the materials used to make them. For example, these wall mount enclosures are typically made of carbon steel. But because such outdoor electrical components are...well, outside, they must be protected from the wind, sun, rain, and snow. Further, no one wants to see a big, ugly metal box hanging from the side of their house, so they must be pleasant to look at. The solution is to paint or powder coat them, yet this adds expense and lead-time to the product. In addition, these finishes—though durable—tend to lose their luster over the long run.
Stainless steel is one alternative. It’s attractive and doesn’t corrode like low carbon steel, although it is relatively expensive, a not-insignificant factor with higher production volumes. Yes, stainless might make great sense for a custom server enclosure in a naval vessel or an outdoor electrical enclosure on a wind farm or solar energy installation, but it is cost-prohibitive for most residential and commercial uses. Now what?
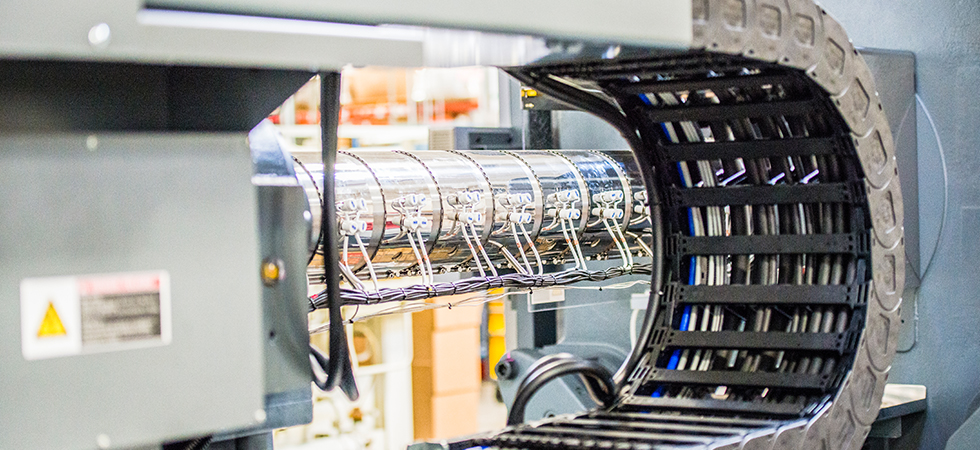
Injection Molding For a High-Tech World
The solution, as with so many other things in the modern world, is plastic, or more specifically, injection-molded plastic. Plastic injection molding of outdoor electrical enclosures, fiber optic boxes, and similar high-tech, high-volume components makes good sense on many fronts. However, the transition to injection molding requires that product engineers learn an entirely new set of design principles, not to mention getting a handle on the wide array of polymers available to them.
Let’s start with the principles, many of which are described in this design for moldability article. Chief among these recommendations is the need for uniform wall thicknesses. Because injection molding works by forcing molten plastic into a machined mold cavity, it’s critical that the material flow in as uniform a manner as possible. If one section is much thinner than another, the plastic in that area will cool more quickly, leading to warpage.
Similarly, overly thick areas are prone to a phenomenon known as sink, which is just as its name describes. For best results, all wall thicknesses should be within 15% or so of nominal, and for unavoidably beefy areas like mounting bosses, use a honeycomb pattern or series of ribs to reduce the amount of material needed without sacrificing strength. Doing so will also serve to decrease molding times and material usage, both of which lead to lower part cost.
Another important design consideration is draft angle. In order to release the electrical enclosure or whatever other part is being produced, plastic injection molds require that the walls of the mold cavity that are perpendicular to the parting line are tapered. The minimum is 1° per side, although 3° is better and 5° optimal. For particularly complex part designs or where surface texturing is applied, even more draft might be necessary. When in doubt, check with your manufacturing partner.
That last recommendation is good advice throughout the design process, because there’s plenty more to plastic injection molding. Sharp corners are generally a no-no. So are sharp transitions from one area to the next. Undercuts increase mold complexity, driving up tooling costs. Company logos and text are fine, but should be placed on a non-draft surface parallel to the parting line. And tall features like ribs and standoffs should have supports placed around them to improve rigidity.
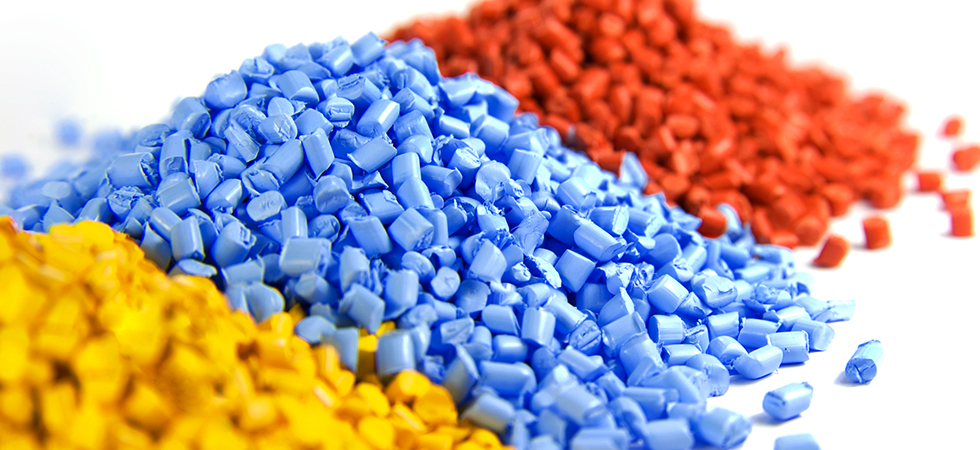
Plastic Material Considerations
Above all, remember that these are not stamped, formed, and welded components. Design considerations for plastic are going to be very different to accommodate for shrinkage, remove any concerns of warpage and hit critical tolerances. That said, plastic injection molding is an extremely viable alternative to traditional sheet metal products, (like electrical enclosures and fiber optic boxes), albeit at the higher production quantities needed to justify the tooling investment.
That brings us to the plastic. What kind are you going to use? To answer that question, you should first make a list of the application requirements. What are the cabinet's "ingress protection" or IP ratings? Is a UL rating for flammability required? How about UV ratings for outdoor exposure? If the enclosure will be used in a medical or food processing environment, is FDA and NSF compliance called for? And what about the product's mechanical properties, or electrical conductivity?
Material selection, it seems, is nearly as complex as the design process. ABS, Nylon, polycarbonate, PVC, and TPU—these are just a few of the more common polymers used for electrical junction boxes, fiber optic enclosures, and other outdoor applications. Compounding matters further are all the different fillers and additives that are available. Materials such as glass and fiber are often mixed in to enhance strength and toughness, while flame retardants, antistatic agents, and UV light absorbers are also quite common
Lastly, don’t forget another big advantage to plastic injection molded parts. Aside from their greater design flexibility, durability, lower weight and piece price, these and other components can be made in a near-rainbow of colors (even though gray, black, and white seem to be the most popular). However, these colorants and all the other additives just described can affect the plastic's moldability, aesthetic values, price tag, and lead-time. Again, talk to your manufacturing partner, preferably one that does both metal and plastic. They’re the experts.
Recent Insights
News
Blog
White Papers