Blog
What To Look For When Sourcing Large Sheet Metal Enclosures
Sheet metal enclosures come in all shapes and sizes. It’s the larger ones, however, that often cause designers and manufacturers the most grief. Here are some things to keep in mind for your next project.
April 5, 2022
If you were one of those kids who built forts out of refrigerator boxes (most of us are), you’re already familiar with a few of the challenges that come with designing and manufacturing large structures. Without reinforcement, the walls and ceiling tend to bow. Moving them around when complete is next to impossible, so building large structures near their final home is a good idea. Duct tape and Elmer’s glue only go so far at holding it all together, making sound joining techniques a must. It’s arduous work, even for the craftiest kids on the block.
Similar statements can be made about super-sized custom metal fabrications. These include data center solutions such as server racks and cabinets. There are steel enclosures for fiber optics, battery storage, and edge computing hardware. Retail kiosks and ATMs are common in this sector, as are OCP (open compute project) solutions. These and other custom sheet metal enclosures serve many critical industrial applications. It’s essential to recognize that no matter how good your design is, not all manufacturers are up to the task.
Experience With Large Fabrications
That’s because, as with cardboard play forts, fabricating large sheet metal enclosures comes with unique challenges vs. making smaller products. For starters, the panels on the sides and backs of fabricated enclosures are often too large to bend on a press brake or require multiple operators (more labor cost). An alternative would be to use a panel bender, which allows the sheet to lie flat during processing, producing a high-quality bend faster and more cost-effectively than the alternatives.
High-Tech Manufacturing and Automated Processes
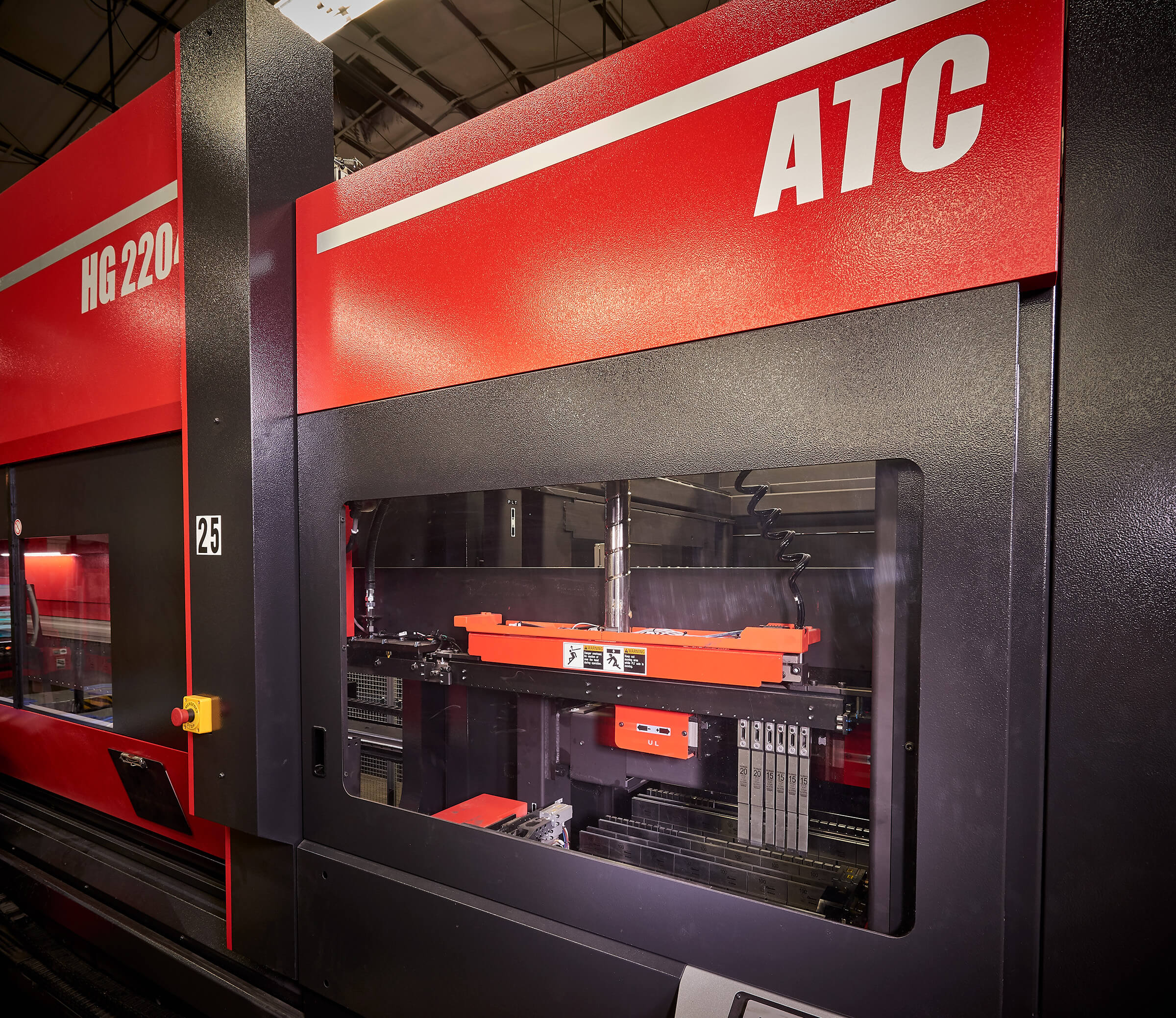
Integrated sheet metal automation is another essential capability to keep in mind. Robotic welding helps to reduce fabricating costs, as do automated material handling systems like conveyors and sheet loaders. These also improve working conditions, eliminating the risk of injury when handling large steel, aluminum, and stainless steel sheets. You want to look for capabilities like in-floor lifting systems or cranes that bring the work to those performing operations like spot welding, riveting, buffing and polishing, and final assembly. Such automated systems help to make the manufacturing process more efficient, giving customers the highest quality products available.
Speed and Flexibility
Of course, not all sheet metal fabrication is automated. Skilled workers will always need to operate a variety of high-tech machinery. Aside from the panel bender already mentioned, press brakes are used to bend the shelves, brackets, and other smaller components needed in something like a custom server rack enclosure. Laser cutting, turret punches, and combo machines also play an important role in blanking, louver forming, notching assembly tabs, and more. The key here is flexibility—handling both large and small parts in the most optimized manner possible.
Finishing New Parts
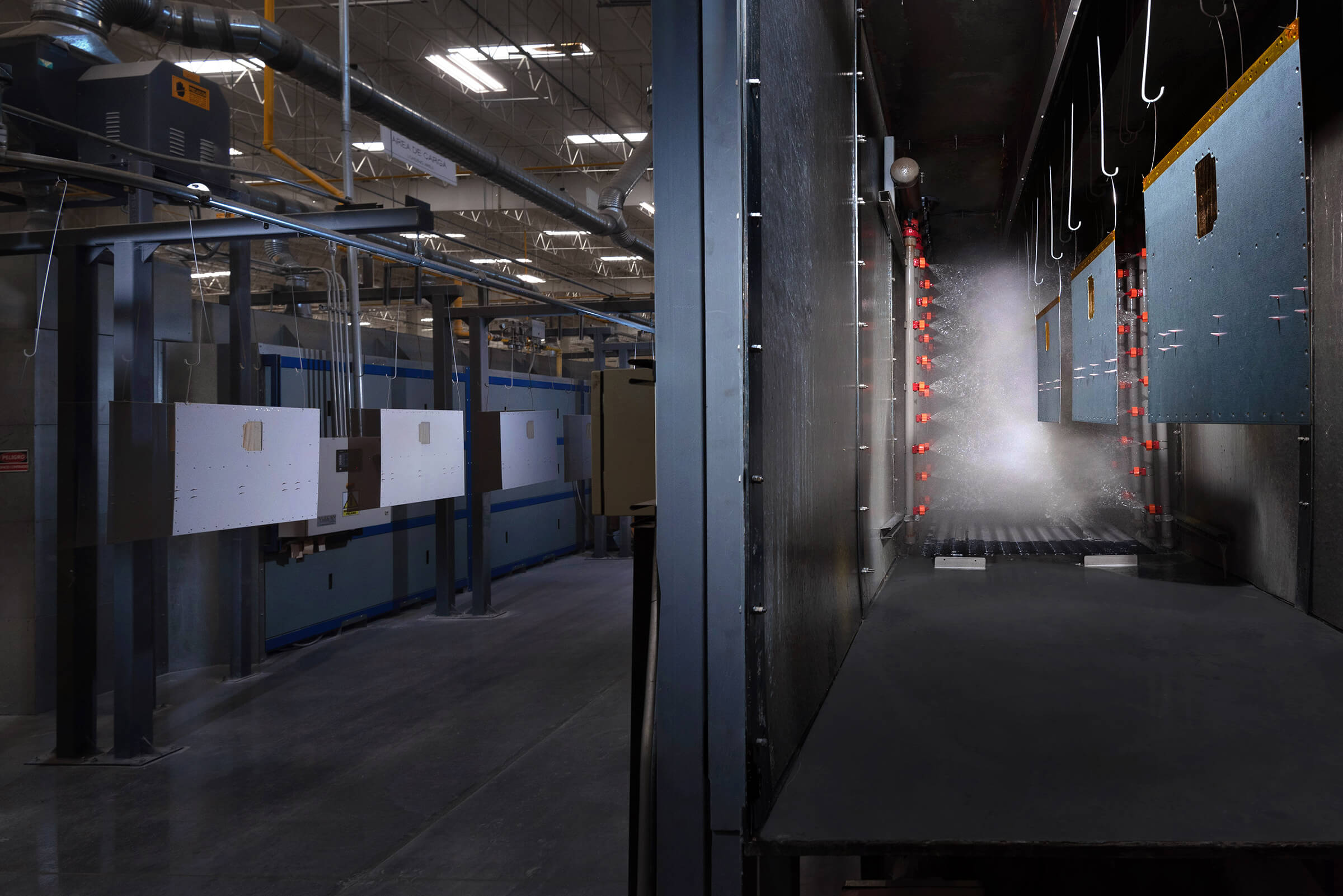
When the various panels and other parts are complete, it’s time to make them pretty. It’s common to use a separate vendor for finishing operations, but a well-equipped manufacturer will have in-house powder coating and painting capabilities. Achieving this level of vertical integration helps to reduce project costs. There’s no risk that parts will be damaged when shipped across town. Lead times are shorter; flexibility is increased.
Proximity to Final Destination
Speaking of shipping across town, how about shipping across the country or even across the ocean? This becomes an increasingly big deal as parts and assemblies get larger. That’s why it’s a good idea to partner with a manufacturer who is relatively close to your facility (not all that different than our cardboard fort example). They should also have experience with packaging and shipping large products or risk more opportunities for damage during shipping. With your manufacturer closer to the part’s final destination (usually the same hemisphere), you can help mitigate the supply chain impact that world events and geopolitical tensions have on your production. These benefits (alongside the lower transport costs) make choosing a manufacturing partner in your own neighborhood a no-brainer.
Product Design and Engineering Services
A supplier's equipment and capabilities are crucial to successful manufacturing, but that’s not all you need to look out for. You will have numerous design guidelines to consider with any product or project. This is why it's vital to find a manufacturing partner willing to work with you on product design. A good one will share their years of experience and make sure you end up with a high-quality product that meets your needs on time and at a fair price. That’s what it’s all about, no matter how large the parts.
Recent Insights
News
Blog
White Papers